“About us” – GIOTTO Project Partners Interview
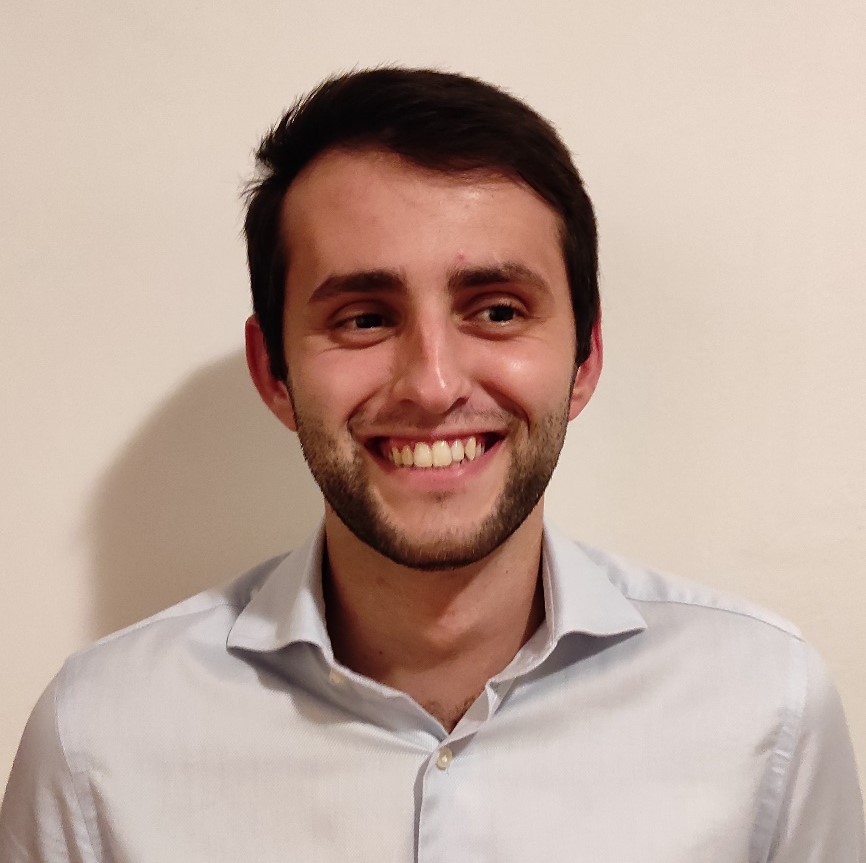
Amedeo Franco Bonatti | Department of information engineering – University of Pisa (Italy)
Currently Post-doc
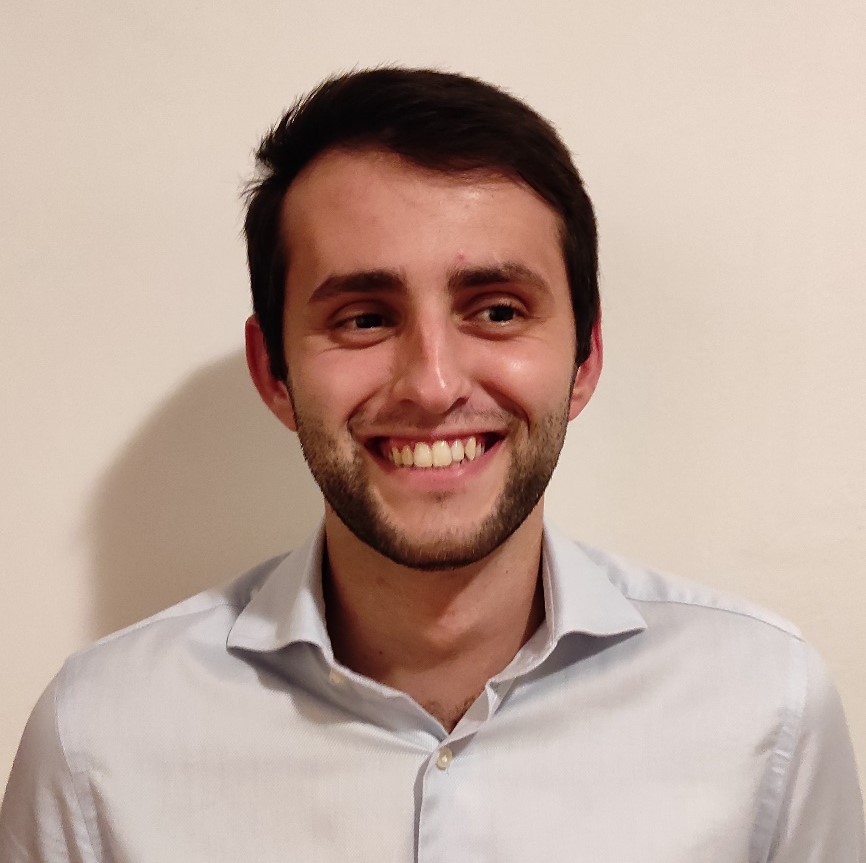
Short Bio & role in the GIOTTO Project
I’m Amedeo Bonatti, a PostDoc researcher at the Research Center “E. Piaggio” and the Department of Information Engineering, University of Pisa. Part of my PhD was carried out in GIOTTO. I received the Bachelor and Master Degree in Biomedical Engineering from University of Pisa, Italy in 2017 and 2019 respectively, and earned my PhD in Information Engineering in February 2023, also at the University of Pisa. My current research activities are focused on the development of advanced, AI-enhanced quality control solutions to accelerate the clinical translation of bioprinting. In GIOTTO, my activities were mainly focused on the design and development of Device 1, a three-dimensional device produced by Additive Manufacturing to treat long bone perisprosthetic fractures correlated with osteoporosis.
What are the main tasks you carried out, and with which results?
In GIOTTO, I firstly assessed the printability of different project materials using multiple Additive Manufacturing technologies relevant for the fabrication of Device 1. Different thermoplastic filaments were produced by UNEW and sent to Pisa for testing using Fused Deposition Modelling (FDM). FDM is the most used 3D printing technology on the market and consists in pushing the filament through a hot zone, were its melted and deposited onto a printing plate in a layer-by-layer fashion. The FDM printing process was optimized for each filament composition in terms of extrusion temperature, printing speed and other relevant printing parameters. The optimized parameters were then used to fabricate scaffolds for in vitro and in vivo testing with high dimensional accuracy, which were sent to the project partners FORTH and NOVAICOS for the biological evaluation. The biological experiments highlighted good overall biocompatibility for the GIOTTO materials processed using FDM printing. Beside FDM, I also characterized the printability of different liquid solutions using inkjet. Inkjet is the technique found in common 2D printers and consists in pushing the material through very thin nozzles to deposit small volume droplets (around 100 pl) of the given biomaterial. During the project, I characterized two main solutions with this technology: the ICOS-Fc solutions from NOVAICOS and the SPIONs solutions from UCM.
Besides printability assessment, I also actively participated in the Device 1 design development from the project start. Together with the UNIPI team, I designed multiple iterations of the Device architecture and geometry, taking into consideration inputs from clinicians, fabrication constraints and results from Finite Element simulations. Finally, I developed a novel bioprinting platform used to fabricate multimaterial and multiscale scaffolds with high control over the quality of the final construct. Specifically, the platform has two bioprinting units: (i) a FDM tool-head for 3D printing scaffolds with thermoplastic filaments; and (ii) a thermal inkjet printhead for depositing biomolecules in specific locations on the printed scaffolds. The platform was used to fabricate high-quality Device 1 samples for in vivo testing in large animals, which are currently on-going.
Has GIOTTO Project changed in some way your career or work?
For sure, the GIOTTO Project has had a major impact on my career. During the project, I had the opportunity to collaborate with research groups all over Europe, exchange new ideas and work together to achieve a common goal. This experience has strengthened my ability to work in a highly multidisciplinary and fast-paced research environment. Moreover, the project has given me the opportunity to present my work at multiple congresses all around Europe, where I had the chance to exchange ideas with other researchers and develop a better understanding of the Tissue Engineering and Biofabrication field.
Leave A Comment